The 25-acre property was improved with 340,000 square feet of industrial buildings, plus railroad spurs and a heliport. It had been previously utilized as a newspaper production facility. A lengthy history of prior releases and piecemeal assessments of fleet fueling identified underground storage tank (UST) systems, auto services and machine shops, clarifiers, and surface releases, some of which had been granted closure by the local (Orange County Health Care Agency, OCHCA) and state (Water Quality Control Board, WQCB) regulatory agencies. During the course of environmental due diligence (Phase I & II ESAs) Targus retrieved and reviewed the entirety of state and county files for the former printing facility and reviewed historical blueprints and other drawings remaining in the abandoned building. Collectively, Targus systematically assessed and closed by removal or risk-based assessment over 20 areas of concern (AOCs) that were identified through Phase II sampling and document review. One of two fuel areas had affected a considerable area of downgradient groundwater, including neighboring property, but had largely been remedied by the former operator and remained in the process of low-threat closure by the county agency.
In addition to petroleum releases, an area affected by release of chlorinated volatile organic compounds (cVOCs) was encountered in proximity to the former centrifugal chiller plant. The cVOC concentrations exceeded both groundwater and soil vapor criteria, after recent policy changes by the WQCB that dramatically reduced soil vapor criteria. Following a soil vapor extraction (SVE) pilot test, Targus worked with the WQCB to establish a plan to move toward regulatory closure through soil vapor mitigation and groundwater monitoring. A passive ventilation system was designed to encompass the sub-slab gravel across the footprint of the soil vapor plume, and a final groundwater monitoring program was established.
The ventilation system is slated for imminent installation in coordination with the building construction team. Upon completion of installation, the sub-slab ventilation (SSV) system will be activated with a permit-exempt regenerative blower for a period of time necessary to demonstrate effective communication across the plume area. Demonstration will be made by mapping the pressure (vacuum) field extension as measured with the roughly two dozen sub-slab vapor pins and soil gas probes. Thereafter, the blower will be removed, sub-slab and soil vapor sampled, and then all penetrations will be sealed. Upon completion of floor sealing, building close-in, and start-up of the heating ventilation and air conditioning (HVAC) system, indoor air will be sampled to document protective indoor air conditions.
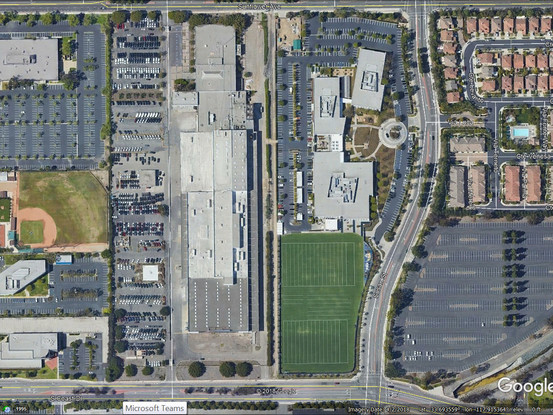
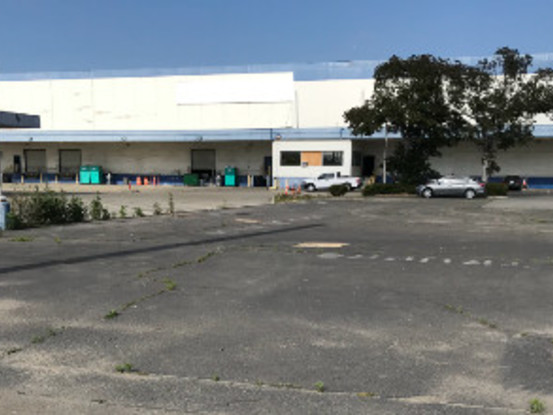
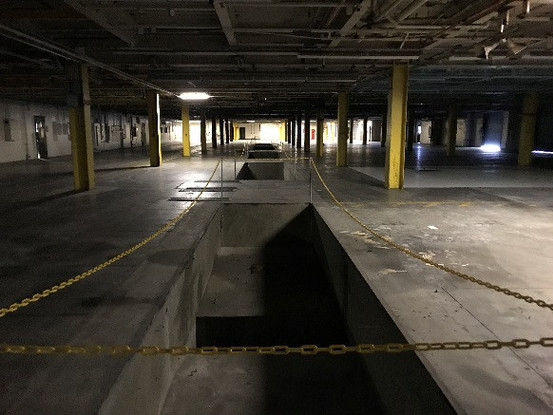
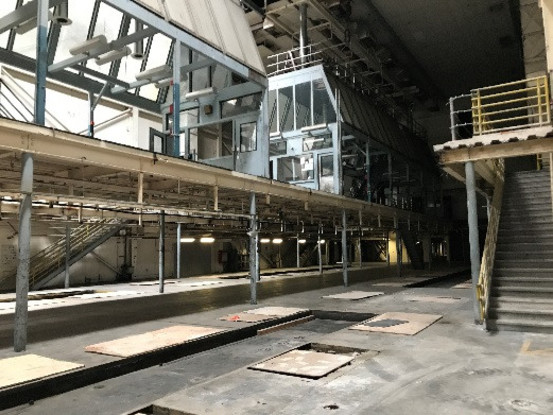